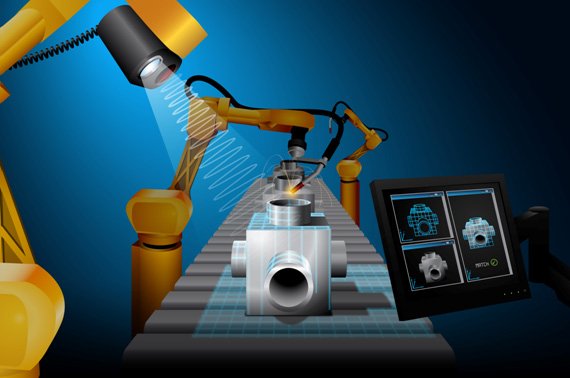
Bringing lightweight components into series production requires profound knowledge of materials – and that is the crux: The behavior of novel materials and structures is difficult to calculate and production processes are subject to different principles than for metal construction.
Researchers at TU Chemnitz are now helping to provide a clearer picture: With the aid of GOM optical 3D metrology, they are able to describe specific material properties, to optimize manufacturing processes and to develop precise-fitting lightweight components for all industrial applications. Beneficiary of this is, among others, the automobile manufacturer BMW: Taking the BMW 7 Series as an example, the researchers from Chemnitz have designed a technology demonstrator for a roof bow made of fiber-reinforced thermoplastics, which is suitable for cost-effective, large-scale series production compared to the thermoset series component.
The Federal Cluster of Excellence “Technology Fusion for Multifunctional Lightweight Structures” MERGE at TU Chemnitz is the first in the field of lightweight construction research in Germany. MERGE researches material science and technological principles for mass-production compatible and resource-saving production of lightweight composite structures. The starting materials include not only specifically modified high-performance polymers and compounds from renewable raw materials, but also thermoplastic prepregs and bionic textile preforms. In addition, the 100-strong MERGE team is involved in the production of components in mixed construction, among others seamless joining of thermoplastic fiber-reinforced composites and metals.
The scientists maintain close links to industry. “We solve specific issues relating to lightweight construction across all sectors. We support our partners at all stages of the lightweight construction process chain: from the selection of suitable materials and material characterization to the construction of lightweight components and tools, simulation, tooling and initial sampling, right up to entry into series production,” reports Prof. Dr. med. Lothar Kroll, director of the Institute of Lightweight Structures and coordinator of the MERGE cluster at the TU Chemnitz.
Optical 3D Metrology As The Backbone Of The Process Chain
In order for the researchers to achieve their goals efficiently, they employ optical 3D measuring systems at all process stages, which measure material samples and components either statically or dynamically depending on the situation. “The use of non-contact measurement technology, which enables non-destructive inspection and testing, saves us time, provides meaningful information about the behavior and nature of materials and components and shows us how best to achieve optimal lightweight components,” says Norbert Schramm, scientific assistant at the Institute of Lightweight Structures.
He demonstrates how the researchers use optical metrology throughout the lightweight construction process using selected practical examples that have been released for publication. “We carry out real fundamental research here, which continuously provides us with new insights; however, many industrial projects are subject to secrecy, because the findings offer the clients an immense competitive advantage,” explains Schramm. Therefore it shouldn’t be a surprise that he can only speak about specific components developed at the Institute of Lightweight Structures at TU Chemnitz in exceptional cases. One such exception is the CFRP roof bow technology demonstrator.
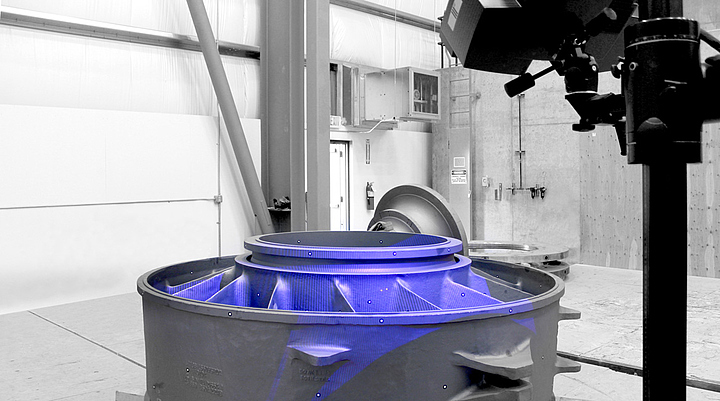
ARAMIS Tests Load Limits of Lightweight Construction Materials
The roof bow is the cross-brace between the B and C pillar of the vehicle and is essential for roof stiffness. For the original component in the current BMW 7 Series, which consists of thermoset CFRP, the goal of the MERGE cluster scientists was to design an alternative made of a thermoplastic composite that provides both technological and economic benefits and is therefore suitable for mass production. The big unknown in this equation: The temperature behavior of continuous fiber-reinforced thermoplastics, which to date has remained almost completely unresearched.
The researchers hoped to shed light on this via temperature-dependent failure analysis. Based on the test results, it should be possible for them to develop a temperature-dependent material profile and describe the derived laws with a design algorithm. Norbert Schramm explained the procedure: “Included in the temperature-dependent failure analysis are carbon fiber reinforced polyamide 6, glass fiber reinforced polyamide 6 and carbon fiber reinforced polyphthalamide. The load limits were investigated based on material samples by applying tensile, compression and shear loads – including combinations thereof – in a typical temperature range of –30 °C to +85 °C for automotive applications.
Never far away: the high-precision ARAMIS measuring sensor from GOM, which has been specially designed for 3D motion and deformation analysis. At up to 2,000 frames per second, the stereo camera system captures the behavior of both individual points and entire surfaces during testing and provides information on 3D displacements, velocity and acceleration as well as surface strain.
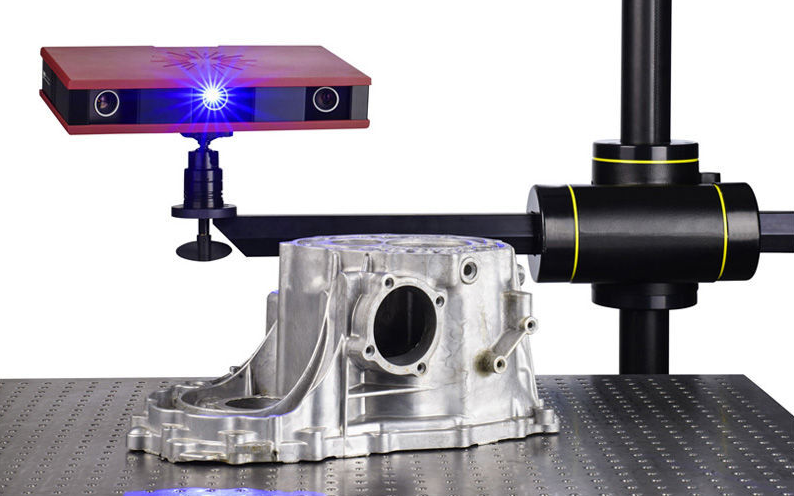
According to Norbert Schramm, the measuring system is particularly useful because it offers both surface and point analysis options. “Local values alone, for example as provided by strain gauges, do not suffice in the case of anisotropic materials with directional mechanical properties. If it is necessary to check both the fiber-dominant mechanical properties of the composite in the fiber direction, and the matrix-dominant properties transverse to the fiber in the load tests, full-surface object information is required. These, together with measurements of specific points, provide us with a comprehensive picture of the state of the material, and even offer information regarding unforeseen effects. ARAMIS generates a dense mesh of easily interpret-able data that provides insight into damage images and their sources.”
The result of these tests was clear: The matrix-dominant properties transverse to the fiber, in particular in the case of carbon and glass fiber reinforced polyamide 6, show a significant temperature influence, which must be taken into account within component design. Here, for example, the shear stiffness and strength in the high temperature range has been reduced by up to 70 percent.
Flexible Measuring Area – Any Geometry, Any Location
But ARAMIS is not only required for determining material characteristics. The Chemnitz researchers also use the mobile deformation and motion sensor during structural tests of the designed lightweight components. Here, the scientists benefit from the system’s flexible measuring area: “With ARAMIS we can test objects of any size and geometry. We have analyzed, among others, side impact beams, instrument panel supports, a snowboard and of course, the roof bow in question for the BMW 7 Series,” explained Norbert Schramm. Often, the mobile system is taken on trips. Then it can take measurements directly in the client’s production environment. “We are called when produced lightweight components have defects and the source of error cannot be identified,” says Schramm. Instead of searching for a ‘needle in a haystack’, the Chemnitz researchers use ARAMIS to perform targeted machine analysis. Schramm remembers one specific case: “We were working for an injection molder who was struggling with film seams on a component. The general assumption was that the load frame guide was to blame. However, the ARAMIS measurements showed that the tool tilted during injection molding.”
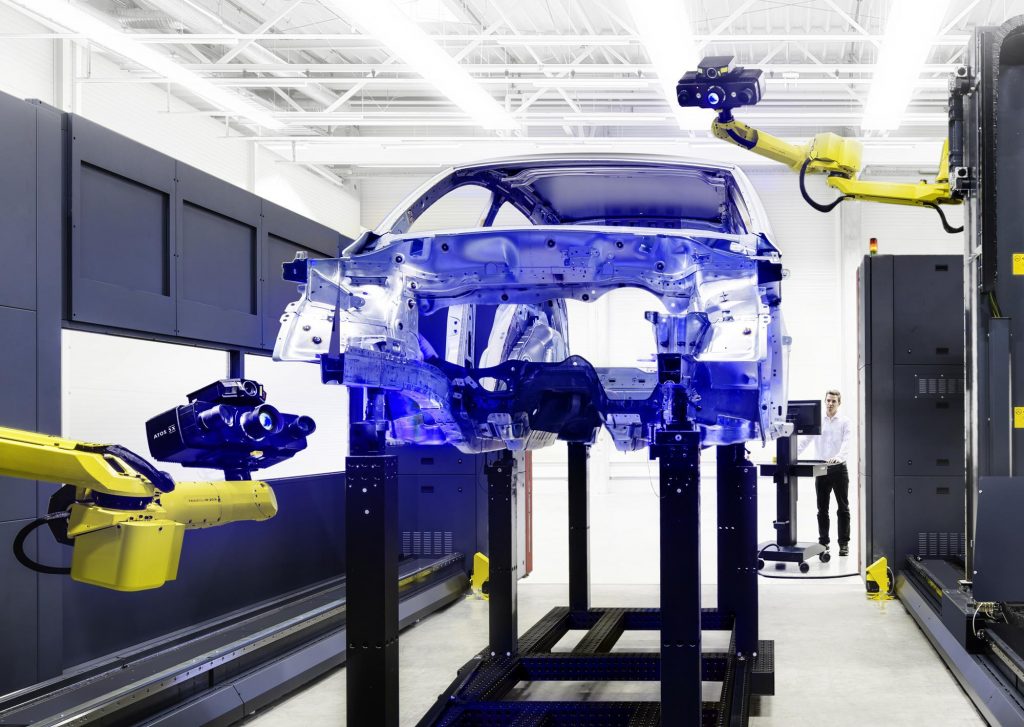
Deformation measurement with ARGUS
Another step back: Before the Chemnitz researchers actively participate in the design of any lightweight component, they take another, this time virtual, look at the material analyzed on the test bench. Using a draping simulation that takes into account the complex interactions of material characteristics, object geometries and manufacturing processes, it is possible to predict how the forming process will affect fiber orientation. This determines all elementary process parameters for the component designer, such as thickness distribution and fiber orientation.
Verification of this simulation is performed in many cases with the help of practical tests. Here, too, optical 3D metrology – in this case the ARGUS measuring system from GOM, which extensively documents the change in shape during forming processes and shows the shearing of the material, is also useful. “We glue the sheet material panels before formation with measuring points, then the forming process is performed and then finally we compare the spatial positions of the points before and after forming.” All results lie within a finely resolved mesh, created by determining the 3D coordinates, and which represents the surface of the measured component.
3D Shape & Dimension Analysis With ATOS
Another piece of the puzzle in the lightweight construction process is 3D shape and dimension analysis of manufactured components and tools. To check production quality, TU Chemnitz relies on the ATOS optical 3D scanner from GOM, which enables precise full-field object digitization in contrast to point-measurement tactile systems. Due to to modern opto-electronics, precise image processing and mathematical algorithms, the ATOS scanner can generate highly accurate images of the specimen.
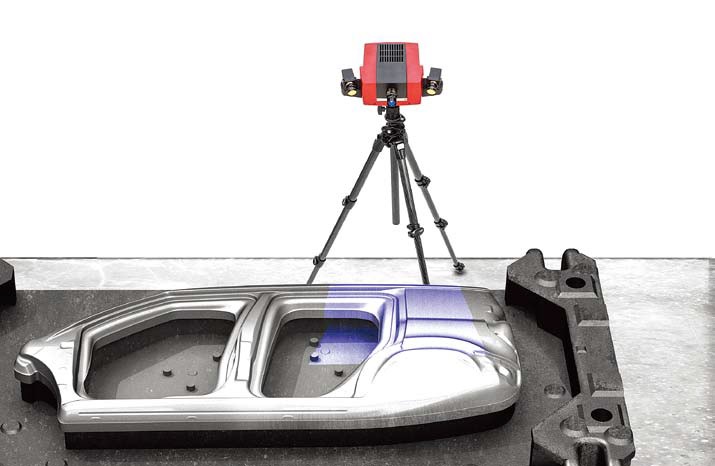
The size of the measuring object is irrelevant. “With ATOS, we scan samples from micro-injection molding as well as complete vehicles,” notes Schramm. Equally broad are the issues that can be resolved with an ATOS measurement: “One case involves comparing component shrinkage, which inevitably occurs in the thermoplastic cooling process, with the simulation. Then we turn again to tool wear: Both halves of the tool are scanned and compared with the CAD data, which makes the wear visible,” says Schramm. The easy-to-understand presentation of measurement results in the reporting is helpful in this case. The deviations between the digitized object and the CAD model are displayed in false colors. This makes the binding points immediately obvious.
The BMW 7 Series roof bow technology demonstrator, mentioned before, was digitized with the ATOS scanner as part of initial sampling. The Chemnitz-based researchers were finally able to realize a significant weight reduction of 45% over the similar steel component of the predecessor model. Further pioneering projects that put conventional components on a diet are in the pipeline. “Optical 3D metrology from GOM will continue to play a key role in this,” concludes Norbert Schramm. “Only in this way can we make reliable material behavior predictions, control the manufacturing process better and inspect components with high precision.”